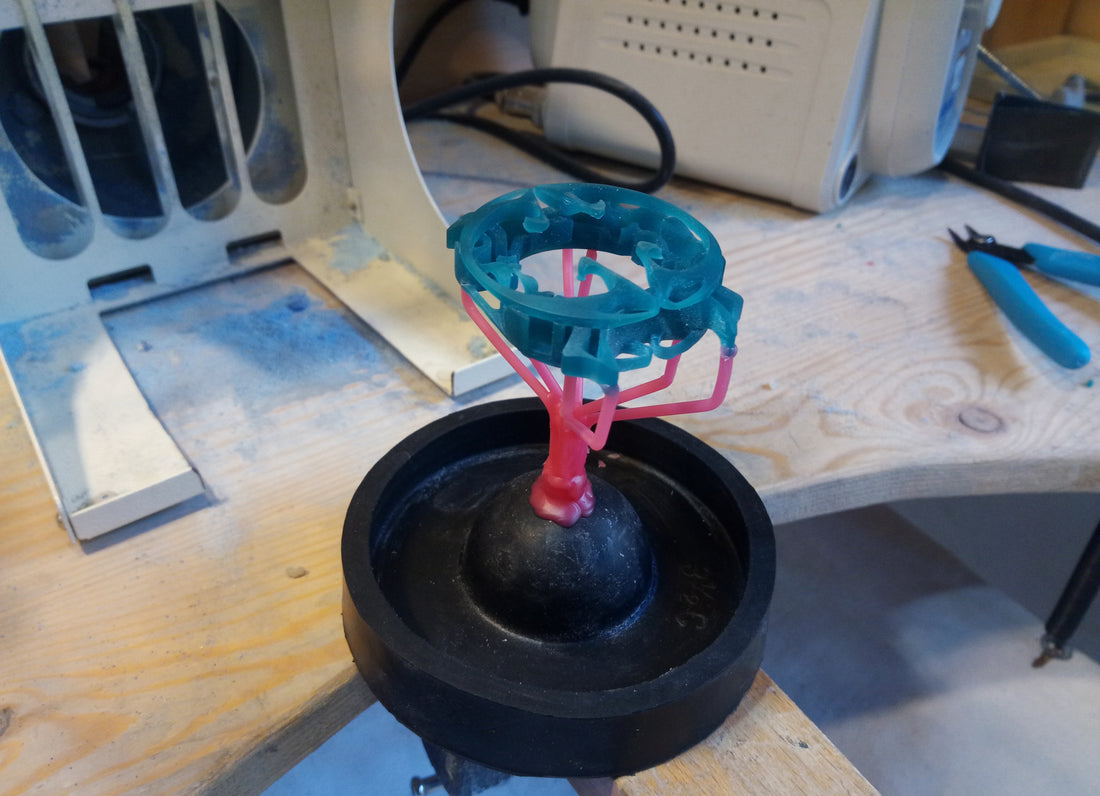
Lost Wax Casting in Watchmaking
Share

The case, dial and buckle of this watch were made using the lost wax casting technique.
The Art of Lost Wax Casting in Watchmaking
Lost wax casting is a precision casting process that allows you to obtain a metal sculpture from a wax model. This ancestral technique is over 6,000 years old. The main steps of this technique are as follows: The piece is sculpted and modeled by hand in wax or printed in 3D with a calcinable resin. This wax or resin is then trapped in refractory plaster. The plaster is put in the oven. The wax melts and leaves its imprint (in the case of resin, it vaporizes). This imprint is filled with precious metal. The workshop is fully equipped to carry out these different steps in-house. We use this process to create precise metal parts (18K gold, 925 silver, brass, etc.) such as watch cases, dials and buckles.

Artisan d'art | Photo of the workstations required for lost wax casting in jewelry
Small illustration of the process in pictures:

Artisan d'art | Simplified process of lost wax casting applied to jewelry
I. The prototype is made by sculpting and/or modeling the wax
II. A casting cone is added to the wax prototype.
III. The prototype is cast in refractory plaster.
IV. The mold is heated so that it hardens and the wax melts.
V. The molten metal is introduced into the mold
VI. The mold is broken to release the metal prototype
VII. The casting cone is cut
VIII. We will then do all the rework: Filing, welding, drilling, polishing, adjusting, etc.
Between the end of step I and step VII, it takes 12 hours to make a quality casting. It is possible to cast several pieces at a time, however I prefer for complex pieces to put only one per mold for an optimal result.

Casting tree of the case of the ALB watch entitled "Khumeia" made using 3D printing